Manômetros.
O que são os Manômetros?
Manômetros são instrumentos de medição utilizados para medir a pressão de líquidos e gases em uma ampla variedade de aplicações. Eles funcionam convertendo a pressão em uma força mecânica que é transmitida a um elemento de medição, que pode ser um tubo em forma de U, um diafragma ou um fole que, por fim, tem o objetivo de transformar essa medida em uma leitura facilmente compreensível para o usuário. Os manômetros são amplamente utilizados em diversas aplicações industriais e comerciais, como em sistemas de aquecimento e refrigeração, processos químicos, sistemas hidráulicos, pneumáticos e de vácuo, entre outros. Os manômetros são essenciais para o monitoramento e controle da pressão em diversas operações, ajudando a garantir a segurança, eficiência e qualidade dos processos.
Como os manômetros funcionam?
Os manômetros obtêm como princípio de sensoriamento em um modo geral a deformação mecânica. Isto ocorre, pois os variados tipos de tecnologia de sensoriamento recebem a pressão e se deformam. Esta deformação ocorre com base no princípio de que a pressão exercida por um líquido ou gás em confinamento é diretamente proporcional à força que ele exerce sobre uma superfície. Em outras palavras, quanto maior a pressão, maior será a força exercida. Desta forma, esta movimentação é transmitida para um sistema de engrenagens que, em contrapartida, transferem o movimento para o ponteiro que indica proporcionalmente a pressão indicada no sistema. São os componentes dos manômetros:
Visor: É a parte dos manômetros que permite visualizar a escala graduada e a posição do ponteiro indicador de pressão.
Ponteiro: O ponteiro é um indicador móvel, que se move sobre a escala graduada do manômetro para indicar a pressão medida.
Placa de discagem: O disco é o elemento de medição dos manômetros, que recebe a escala graduada, sendo ela responsável por gerar a indicação da pressão no sistema. Engrenagens: Algumas vezes, os manômetros possuem sistemas mecânicos, como engrenagens, que amplificam o movimento do disco e movem o ponteiro com maior precisão.
Tecnologia de sensoriamento: O elemento sensor é o elemento de medição dos manômetros, que recebe a pressão e se deforma, gerando uma força que é transmitida para o ponteiro indicador.
Conexões mecânicas: São usadas para conectar os manômetros ao sistema onde a pressão será medida, permitindo que o fluido de processo exerça pressão sobre o disco ou elemento sensorial.
Vedações: As vedações são peças que garantem a estanqueidade dos manômetros e evitam vazamentos de fluidos, gases ou ar. Elas são geralmente feitas de materiais como borracha, silicone ou teflon e podem ser encontradas em diversas partes dos manômetros, como nas conexões ou no sensoriamento.
Características construtivas dos manômetros
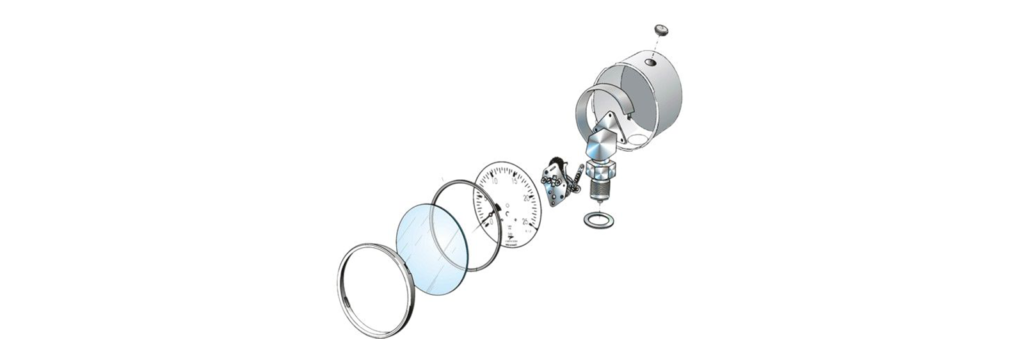
O funcionamento do vacuostato ocorre como um interruptor elétrico em uma pressão negativa, pressão essa que fora determinada previamente, ou seja, atua na abertura ou no fechamento de um contato elétrico sinalizando quando determinada pressão negativa for atingida.
Esses componentes são utilizados em vários setores da indústria visando principalmente processos de automação industrial, como em linhas de produção automatizadas, por exemplo. Também são muito utilizados no setor automotivo, atuando no sistema de controle de bomba de vácuo de veículos elétricos, veículos diesel e veículos a gasolina.
A precisão desses dispositivos é de extrema importância pois impacta diretamente no funcionamento de sistemas complexos com vários componentes. A descalibração ou defeito no dispositivo pode impactar em perda de produtividade ou até mesmo comprometer a inteira segurança do local onde a aplicação fica localizada. Então, realizar inspeções, manutenções ou até mesmo a substituição dos vacuostatos devem ser considerados processos de alta relevância. Acima de tudo, a escolha de um vacuostato com boa procedência vai garantir segurança, produtividade e maior durabilidade de todo o sistema.
Orientação da instalação dos manômetros
A orientação de instalação dos manômetros é de extrema importância para sua característica construtiva e aplicabilidade em geral para o local em que ele deve ser instalado. Usualmente, se ele tiver como finalidade ser um mostrador de painel, possuirá a orientação horizontal (angular), e se ele for um elemento de processo possuirá a orientação vertical (reta). Entretanto, não se trata de fato de uma regra: a orientação do instrumento deve ser a mais eficiente em termos de ergonomia, e evitar os possíveis erros como, por exemplo, o de paralaxe.
Conexões ao processo
As conexões em manômetros podem ser realizadas das formas mais variadas possíveis, como através de uma conexão roscada, podem ser fixados através de flanges ou garra de fixação. Ainda há possibilidade de acessórios que ficam entre os manômetros e o processo, como tubo sifão, selo diafragma e selo tri-clamp. As conexões roscadas seguem os padrões de roscas paralelas e cônicas a depender de cada aplicação.
As roscas cônicas ocasionalmente seguem os padrões NPT e BSPT, muito comuns em produtos de fabricação ou projeto norte-americano, devido ser estabelecido pela ANSI (American National Standarts Institute), bem como pela ASME (American Society of Mechanical Engineers). Estas conexões possuem um diâmetro que vai se afunilando ligeiramente de um extremo ao outro da rosca e são vedadas através do princípio do arredondamento, isto é, através do aumento do diâmetro através dos fios de rosca. Entretanto, para que haja uma vedação ainda mais eficiente não é incomum a utilização de fita Teflon® ou travas rosca, por exemplo.
Por outro lado, as roscas paralelas seguem padrões como BSPP (British Standard Pipe Parallel). Este tipo de conexão pode ser frequentemente chamado também de rosca métrica, pois segue os padrões internacionais de medida. Estas roscas possuem um diâmetro constante com roscas paralelas. Para vedação deste tipo de conexão, sempre se faz necessária a utilização de anéis de vedação, sejam eles metálicos ou de borracha, internos ou externos. Sem a adição destes elementos, esta categoria de roscas não obtêm uma vedação eficaz.
Outros tipos de conexões poderão ser aplicadas a depender da necessidade do cliente. Por exemplo, se houver uma lata temperatura no processo, pode-se adicionar um tubo capilar; no caso de reposicionamento, basta adicionar um sifão; também é possível a adição de adaptadores em casos que a conexão do medidor não é adequada para o processo, dentre outros diversos tipos de conexões disponíveis no mercado.
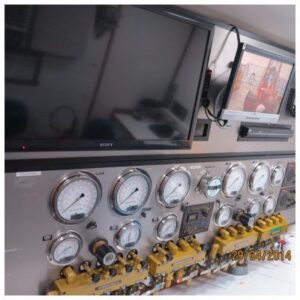
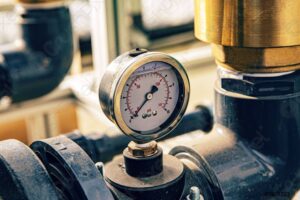
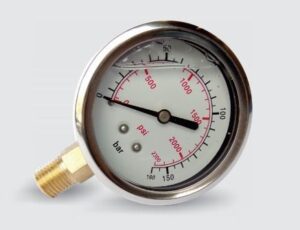
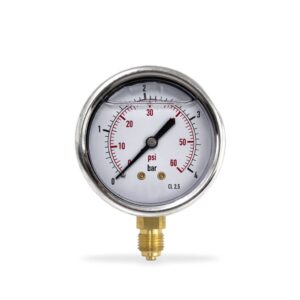
Tamanho dos manômetros
O tamanho dos manômetros geralmente se refere ao tamanho da escala de medição, que pode variar desde pequenos manômetros portáteis até manômetros industriais maiores. O tamanho dos manômetros é escolhido de acordo com a aplicação específica e a faixa de pressão a ser medida.
Para aplicações com pressões baixas, os manômetros com escalas menores são preferíveis, pois podem fornecer leituras mais precisas e sensíveis. Já em aplicações com pressões mais altas, manômetros com escalas maiores podem ser necessários para suportar as altas pressões.
Além disso, o tamanho dos manômetros também pode afetar sua portabilidade e facilidade de leitura. Manômetros maiores podem ser mais difíceis de transportar e operar, enquanto os manômetros menores são mais portáteis e fáceis de manusear.
Manômetros para aplicações químicas e sanitárias
Os manômetros para aplicações químicas e sanitárias são projetados para atender às necessidades específicas de medição de pressão em ambientes químicos ou em processos sanitários. Esses manômetros são frequentemente utilizados em indústrias farmacêuticas, alimentícias, de bebidas, de cosméticos, entre outras, onde a higiene e a segurança do produto são críticas.
Os manômetros para aplicações químicas geralmente são feitos de materiais resistentes à corrosão, como aço inoxidável ou ligas especiais, que podem suportar produtos químicos agressivos. Eles são geralmente equipados com juntas de vedação química para evitar vazamentos e são construídos de forma a permitir a limpeza e a esterilização.
Os manômetros para aplicações sanitárias, por sua vez, são projetados para atender aos padrões de higiene e segurança necessários em processos sanitários. Eles são frequentemente usados em sistemas de purificação de água, tratamento de esgoto, processamento de alimentos, entre outros. Esses manômetros são geralmente construídos com materiais de grau alimentício, como aço inoxidável polido e são equipados com juntas de vedação sanitária para garantir que não haja contaminação cruzada entre os processos.
Manômetros com preenchimento líquido
Manômetros com preenchimento líquido são aqueles que possuem um líquido, geralmente glicerina ou óleo, preenchendo o espaço entre o elemento sensorial e o visor. Esse líquido age como um amortecedor de vibrações e oscilações do elemento sensorial, o que reduz o desgaste do equipamento e melhora a precisão das leituras.
O líquido também ajuda a lubrificar as partes internas do manômetro, evitando a corrosão e prolongando a vida útil do equipamento. Além disso, o preenchimento líquido ajuda a minimizar os efeitos de temperaturas extremas, pois o líquido atua como um regulador térmico.
Os manômetros com preenchimento líquido são frequentemente usados em aplicaçõesque exigem alta precisão, como em processos industriais ou em laboratórios. Eles também são ideais para ambientes com vibrações, choques ou oscilações, pois o líquido absorve esses movimentos e reduz o desgaste do equipamento.
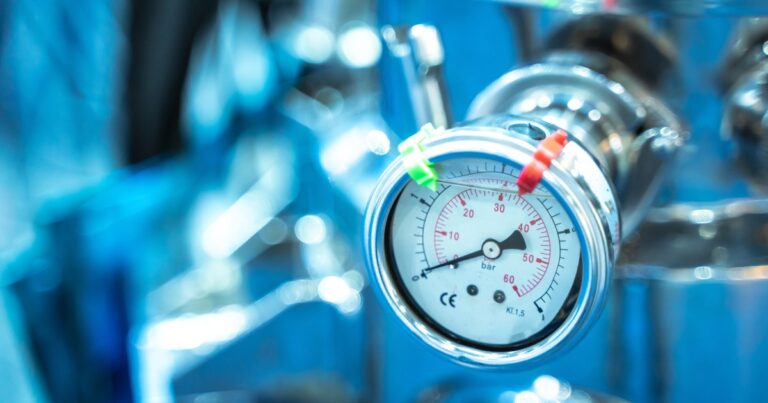
Tecnologia de sensoriamento dos manômetros
Manômetros do tipo bourdon
Manômetros do tipo Bourdon ou “tipo C” são medidores que, de um modo geral, utilizam-se da deformação de um tubo de cobre. O tubo é fixado na tomada de pressão através de uma solda (a depender da aplicação, de um modo geral é uma solda em estanho) e na sua outra ponta é ligado em um sistema de engrenagens responsável pela transmissão do movimento recebido.
Ao receber o fluido pressurizado e confinado em seu interior, o tubo se deforma a depender da pressão injetada. Quanto maior a pressão dentro do limite elástico deste tubo ele se deforma, elevando a haste de fixação e movimentando o sistema de engrenagens que, por sua vez, transfere o movimento para o ponteiro, que indicará no visor a pressão exata do sistema.
O que de fato definirá as características desta categoria de indicadores de pressão será a sua construção e os materiais utilizados para a mesma, por exemplo: se a solda utilizada for de estanho, o mesmo será aplicável apenas a fluídos de no máximo 60°C; caso seja outra configuração, obteremos outros resultados. No entanto, de um modo geral, podem ser aplicados até 270°C e em pressões de 0,6 a 6000 Bar.

Manômetros do tipo diafragma
Esses manômetros consistem em um diafragma flexível que é deformado pela pressão do fluido, o que resulta em uma leitura de pressão no indicador do manômetro. Os manômetros de diafragma são frequentemente usados em sistemas hidráulicos e pneumáticos, bem como em aplicações industriais, médicas e laboratoriais. Eles são valorizados por sua precisão, durabilidade e capacidade de lidar com fluidos corrosivos ou tóxicos. No entanto, eles podem ser afetados por variações de temperatura e vibrações, o que pode afetar a precisão das leituras. Os manômetros de diafragma podem ser encontrados em uma variedade de formatos, incluindo modelos digitais e analógicos, e estão disponíveis em diferentes escalas de pressão para atender a uma ampla gama de aplicações.
Manômetros do tipo fole
Os manômetros do tipo fole são instrumentos de medição de pressão, que utilizam um fole metálico para medir a pressão de fluidos em um sistema. O fole é um componente tubular que se expande ou contrai com as variações de pressão do fluido. A expansão ou contração do fole é, então, transmitida para um indicador de pressão, que exibe a leitura da pressão. Os manômetros do tipo fole são usados em aplicações em que é necessário medir pressões muito baixas ou pressões negativas, onde outros tipos de manômetros não seriam capazes de fornecer leituras precisas. Eles são frequentemente usados em sistemas de vácuo, laboratórios e indústrias, como aeroespacial e farmacêutica. Os manômetros do tipo fole podem ser encontrados em uma variedade de tamanhos e escalas de pressão, desde instrumentos portáteis de mão até grandes dispositivos de medição industrial. Eles são valorizados por sua precisão, durabilidade e capacidade de suportar temperaturas extremas e ambientes corrosivos. No entanto, eles podem ser afetados por variações de temperatura e vibrações, o que pode afetar a precisão das leituras.
Classes de precisão dos manômetros
Os manômetros podem ser classificados de acordo com sua precisão, geralmente expressa em porcentagem da escala total do manômetro. A norma ABNT NBR 14105- 1:2011 estabelece oito classes de precisão para manômetros. São elas:
Classe A4: Precisão de ±0,1% da faixa total do manômetro.
Classe A3: Precisão de ±0,25% da faixa total do manômetro.
Classe A2: Precisão de ±0,5% da faixa total do manômetro.
Classe A1: Precisão de ±1,0% da faixa total do manômetro.
Classe A: Precisão de ±1,6% da faixa total do manômetro.
Classe B: Precisão de ±3/2/3% da faixa total do manômetro.
Classe C: Precisão de ±4/3/4% da faixa total do manômetro.
Classe D: Precisão de ±5/4/5% da faixa total do manômetro.
Cada classe de precisão é adequada para aplicações diferentes, sendo a classe A indicada para aplicações que requerem alta precisão, como em laboratórios, enquanto a classe C é adequada para aplicações menos críticas, como em sistemas de refrigeração, por exemplo.
Outro fator relevante definido na norma ABNT NBR 14105-1:2011 é o diâmetro nominal do manômetro em relação a sua classe de exatidão, definido da seguinte maneira:

É importante observar que a escolha da classe de precisão adequada para cada aplicação depende de diversos fatores, como a faixa de pressão a ser medida, as condições ambientais, a exigência de precisão da aplicação, entre outros. Além disso, é essencial garantir que o manômetro seja instalado, calibrado e mantido de acordo com as normas e procedimentos recomendados para garantir sua operação segura e confiável.

Como realizar a leitura de forma adequada dos manômetros
Realizar a leitura dos manômetros corretamente é importante para garantir que as leituras de pressão sejam precisas e confiáveis. Para ler os manômetros de forma adequada, siga os seguintes passos:
Certifique-se de que o manômetro está na escala de pressão correta. Alguns manômetros têm escalas diferentes, então verifique se você está lendo na escala correta para sua aplicação. predominância.
Verifique se o ponteiro está posicionado em zero quando não há pressão no sistema. Caso contrário, ajuste o zero do ponteiro para a posição correta.
Verifique se há uma boa iluminação para visualizar a escala com clareza.
Olhe para o ponteiro do manômetro e determine onde ele está posicionado na escala. Certifique-se de ler a posição do ponteiro com precisão. Algumas escalas têm incrementos muito pequenos, portanto, é importante ler a escala com cuidado.
Anote a leitura do manômetro, se necessário, ou registre a leitura em um sistema de monitoramento.
Lembre-se de que as leituras de um manômetro podem ser afetadas por fatores como temperatura, vibrações ou condições do fluido. É importante monitorar esses fatores para garantir a precisão das leituras. Além disso, é importante seguir as instruções do fabricante para o uso e manutenção do manômetro para garantir sua precisão e confiabilidade ao longo do tempo.
Como especificar os manômetros
Para especificar os manômetros, é necessário considerar alguns fatores importantes. A seguir, apresentamos algumas informações que devem ser consideradas:
1. Faixa de medição: A faixa de medição é a amplitude de pressão que o manômetro será capaz de medir. Ela deve ser escolhida de acordo com as necessidades da aplicação.
2. Precisão: A precisão é um fator importante a ser considerado, pois afeta diretamente a qualidade das leituras do manômetro. É importante escolher um manômetro com a classe de precisão adequada para a aplicação.
3. Diâmetro do visor: O diâmetro do visor afeta a facilidade de leitura do manômetro. É importante escolher um diâmetro que permita uma boa visualização da escala graduada.
4. Tipo de conexão: O tipo de conexão deve ser especificado de acordo com o sistema onde o manômetro será instalado. Existem diversos tipos de conexões, como rosca, flange, solda, entre outros.
5. Material de construção: O material de construção é um fator importante a ser considerado, pois afeta a resistência do manômetro e sua compatibilidade com o fluido de processo. É importante escolher um material que seja compatível com a aplicação e resista às condições ambientais.
6. Tipo de elemento sensorial: O tipo de elemento sensorial deve ser especificado de acordo com a aplicação. Existem diversos tipos de elementos sensoriais, como diafragma, fole, Bourdon, entre outros.
7. Tipo de preenchimento: Caso necessário, o tipo de preenchimento também deve ser especificado, como o preenchimento líquido para aplicações que exigem maior precisão ou proteção contra vibrações.
8. Certificação e normas: É importante escolher manômetros que atendam às normas e padrões aplicáveis, como as normas EN 837-1 e ABNT NBR 14105-1. Certificações como a ISO 9001 também são um indicador de qualidade do produto. Ao considerar esses fatores, é possível especificar um manômetro adequado para a aplicação desejada.